SPXU series scraper heat exchanger
SPXU series scraper heat exchanger unit is a new type of scraper heat exchanger, can be used to heat and cool a variety of viscosity products, especially for very thick and viscous products, with strong quality, economic health, high heat transfer efficiency, affordable features.
• Compact structure design
• Robust spindle connection (60mm) construction
• Durable scraper quality and technology
• High precision machining technology
• Solid heat transfer cylinder material and inner hole processing
• Heat transfer cylinder can be removed and replaced separately
• Shared gear motor drive – no couplings, belts or pulley
• Concentric or eccentric shaft mounting
• Comply with GMP, CFIA, 3A and ASME design standards, FDA optional
Product processed by SSHEs.
The scraper heat exchanger can be used in almost any continuous process for pumping fluid or viscous fluid, and can have the following applications:
Industrial application
Heating
Aseptic cooling
Cryogenic cooling
Crystallization
Disinfection.
Pasteurization
Jelling
Product specification
Parts for SPXU scraper heat exchangers can be manufactured in a variety of configurations and materials, so each heat exchanger unit can be personalized to meet the specific process requirements of each application. Products comply with GMP, CFIA, 3A and ASME design standards and can be provided with FDA certification.
• Drive motor power from 5.5 to 22kW
• Wide range of output speed (100~350 r/min)
• Chromium-nickel-plated carbon steel and 316 stainless steel heat transfer tubes designed for enhanced heat transfer
• Standard stainless steel or plastic scraper, custom plastic scraper that can detect metal
• Spindle diameters based on fluid characteristics (120, 130 and 140mm)
• Single or double mechanical seal is optional
Photos of SSHEs
Dielectric interlayer
Dielectric interlayers of scraper heat exchangers for liquid, steam or direct expansion refrigeration
Jacket Pressure of dielectric sandwich
232 psi(16 MPa) @ 400° F (204° C) or 116 psi(0.8MPa) @ 400° F (204° C)
Product Side Pressure. Product side pressure
435 psi (3MPa) @ 400° F (204° C) or 870 psi(6MPa) @ 400° F (204° C)
Heat transfer cylinder
• Thermal conductivity and wall thickness are key design considerations in selecting heat transfer tubes. The cylinder wall thickness is precisely designed to minimize heat transfer resistance while maximizing structural stability.
• Pure nickel cylinder with high thermal conductivity. The inside of the cylinder is plated with hard chrome and then ground and polished to make it smooth to resist abrasion from scrapers and grinding products.
• Chromium-plated carbon steel tubes provide high thermal conductivity at a reasonable cost for products such as peanut butter, shortening and margarine.
• Stainless steel tubes specifically designed to enhance heat transfer for acidic products and provide flexibility in the use of cleaning chemicals.
strickle
Scrapers are arranged in staggered rows on the shaft. The scraper is secured to the shaft of the scraper heat exchanger by a robust, durable, specially designed “universal pin”. These pins can be quickly and easily removed and the scraper replaced.
seal
Mechanical seals are specially designed to be easy to assemble and maintain, and to ensure reliable operation.
The heating rate of the product and the residence time in the heat exchanger are controlled by the volume of the equipment. Heat exchangers with small diameter shafts provide large annular gaps and extended residence times, and can handle bulk products and products with large particles. Heat exchangers with large diameter shafts provide smaller annular gaps for high speeds and turbulence, and have higher heat transfer rates and shorter product residence times.
Drive motor
Choosing the right drive motor for the scraper heat exchanger provides the best performance in each individual application, ensuring that the product is vigorously stirred and continuously scraped off the heat transfer wall. The scraper heat exchanger is equipped with a direct-drive gear motor with multiple power options to provide optimal performance for specific applications.
Inner structure of SSHEs
Heat-sensitive product
Products degraded by prolonged exposure to heat can be treated effectively in scraper heat exchangers. The scraper prevents the product from remaining on the heat transfer surface by constantly removing and renewing the film. Because only a small amount of the product is exposed to the overheated surface for a short period of time, burns can be minimized or eliminated to avoid coking.
Sticky product
Scraper heat exchangers handle sticky products more efficiently than traditional plate or tube heat exchangers. The product film is continuously scraped off the heat transfer wall to generate extremely high heat transfer rates. Continuous agitation will cause turbulence, making heating or cooling more uniform; The pressure drop can be effectively controlled by the product annulus area; Agitation can eliminate stagnant areas and product accumulation; And it’s easier to clean.
Granular product
In scraper heat exchangers, it is easy to handle products with particles that tend to clog conventional heat exchangers, a problem that is avoided in scraper heat exchangers.
Crystalline product
Crystallized products are ideal for processing scraper heat exchangers. The material crystallizes on the heat transfer wall, and the scraper removes it and keeps the surface clean. The great supercooling degree and strong agitation can form a fine crystal nucleus.
Chemical processing
The chemical, pharmaceutical and petrochemical industries can use scraper heat exchangers in many processes, which can be divided into four broad categories.
1. Heating and cooling: For scraper heat exchangers, handling very sticky materials is not a problem. Scrape the product film from the surface of the heat pipe or cold pipe several times per minute to prevent the formation of a scale or frozen layer to prevent further heat transfer. The total product flow area is large, so the pressure drop is minimal.
2. Crystallization: The scraper heat exchanger can be used as a gap cooler to cool the material to the subcooling temperature, at which point the solute begins to crystallize. Circulating through the heat exchanger at a high flow rate produces crystal nuclei, which grow to separate after reaching a final temperature. Wax and other fully cured products can be cooled to the melting point in a single operation, then filled into a mold, deposited on a cold strip or granulated using other equipment.
3. Reaction control: scraper heat exchangers can be used to drive chemical reactions by controlling the heat supply. For exothermic reactions, heat exchangers can remove the reaction heat to prevent product degradation or adverse side reactions. The heat exchanger can operate at extremely high pressures of 870 psi (6MPa).
4. Whipped/Inflated products:
The scraper heat exchanger transmits a strong mixing effect to the product as it flows along the rotating axis, so gas can be mixed into the product while heating or cooling it. Inflatable products can be made by adding gas rather than relying on a chemical reaction to produce bubbles as a by-product.
Processed product
Typical application of scraper heat exchanger
High viscosity material
Surimi, tomato sauce, custard Sauce, chocolate sauce, whipped/aerated products, peanut butter, mashed potatoes, starch paste, sandwich sauce, gelatin,Mechanical boneless minced meat, baby food, nougat, skin cream, shampoo, etc.
Heat sensitive material
Egg liquid products, gravy, fruit preparations, cream cheese, whey, soy sauce, protein liquid, chopped fish, etcCrystallization and phase transformationSugar concentrate, margarine, shortening, lard, fudge, solvents, fatty acids, petroleum jelly, beer and wine, etc
Granular material
Minced meat, chicken nuggets, fish meal, pet food, preserves, fruit yogurt, fruit ingredients, pie filling, smoothies, pudding, vegetable slices, Lao Gan Ma, etcViscous materialCaramel, cheese sauce, lecithin, cheese, candy, yeast extract, mascara, toothpaste, wax, etc
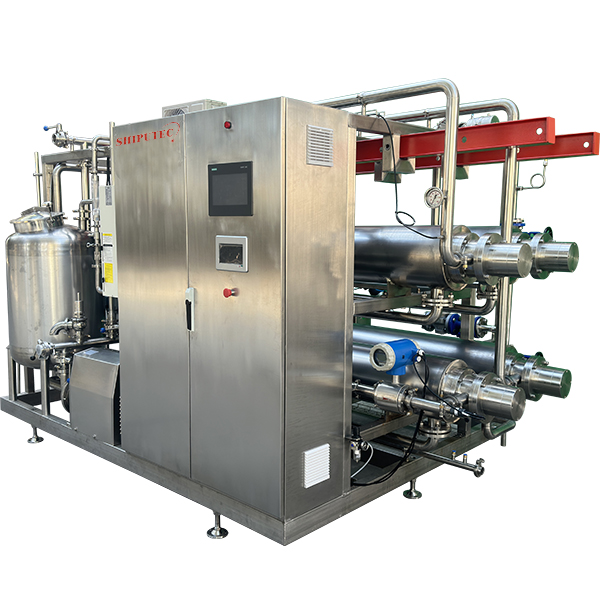

